Wiscraft’s manufacturing processes are similar to those of our competitors, however we go the extra mile to ensure robust processes! Our engineering, training and supervisory personnel utilize their vast experience and knowledge to incorporate lean methodologies into each workstation. Because of our workforce’s special needs, work instructions, development and fabrication of fixtures and various other accommodations, are created with the utmost attention to detail to meet our customer’s quality standards.
Since the implementation of our ISO 9001:2008 certification, our measured outcomes for quality, on-time delivery, production efficiencies and inventory control have improved significantly. Wiscraft’s process improvements are achieved by focusing on concepts like workplace organization, continuous flow work cells, standardized work instructions, and tailored training to meet individual employee needs, as well as fixtures and high tech accommodations.
The implementation of 5-S has helped employees to organize and maintain a clean and safe work environment. A significant element of successful continuous flow cells is the availability of
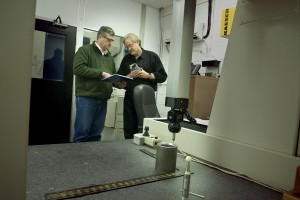
standardized work instructions. To accommodate the varied degrees of employee vision challenges, the detailed work instructions are available in large print and audibly via mobile carts with screen reading technology. The instructions also include quality information to allow every production employee to take ownership of products they create. In addition to individual responsibility for quality during production, lead people and supervisors perform a final quality check before the product is packaged and shipped.
Annual maintenance of Wiscraft’s ISO 9001:2008 registration is another indication of our dedication to operational excellence on all levels. The initial October 2002 registration highlighted Wiscraft as the first U.S. manufacturer employing people who are legally blind to be registered to the new ISO 9001:2000 standard. Wiscraft is committed to excellence through continuous improvement of our management system and work environment; which is reflected in customer satisfaction, documented training outcomes and improved employee retention.
Recently Wiscraft implemented an enterprise-wide paperless initiative. To date, three mobile computing stations have been deployed in our manufacturing area to replace paper based processes. The first use provides work instructions electronically accessible to individuals with all levels of sight using advanced screen reading technology. The station is mobile, allowing it to be moved to any
workstation where training is required. This process eliminated paper manuals and provided up-to-date training and instruction materials. The goal is to eliminate training from “memory” by all levels of trainers. This increases quality and efficiency in the training process.
Wiscraft utilizes a monthly Quality Team meeting to bring forth new ideas, track progress of current initiatives and monitor success of prior improvements. The attitude is always positive. The improvements focused on process. This environment allows for full staff participation.